More than 10 years of experience in creative Ultrasonic solutions!
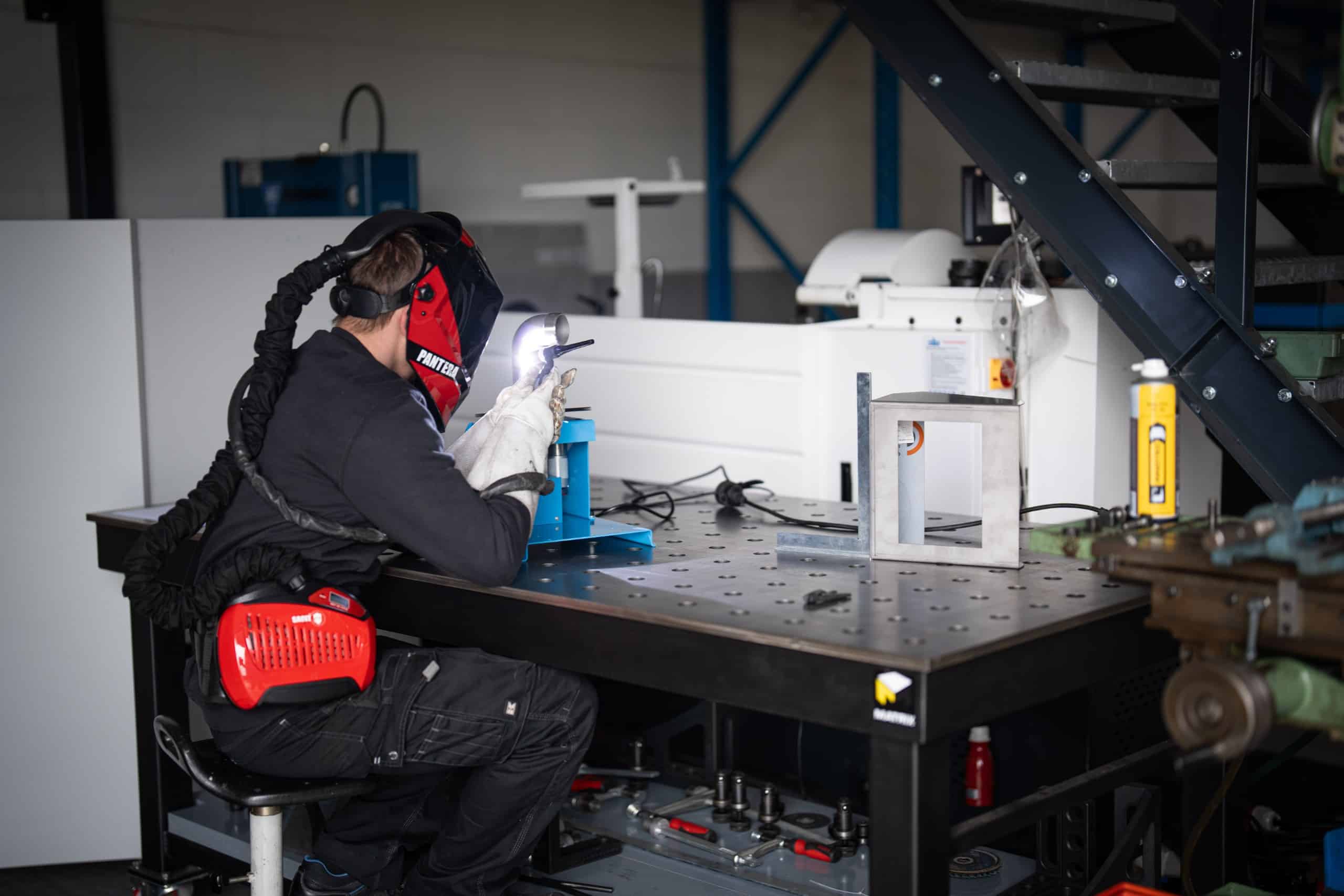
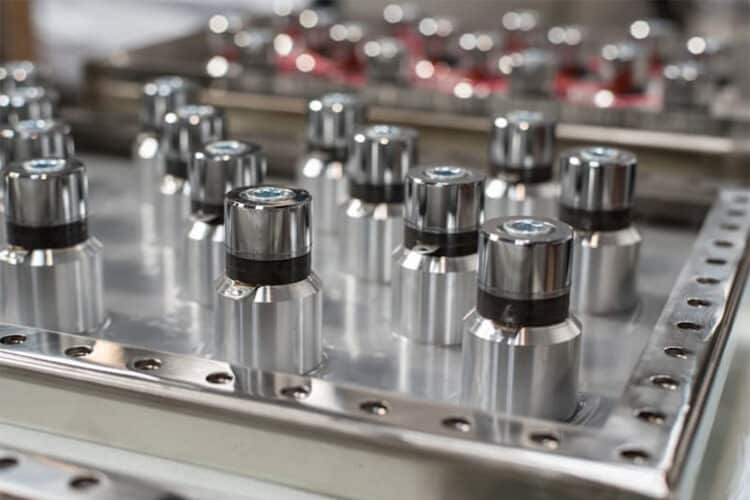
Technology behind Ultrasonic
The vibrations of high-frequency sound waves in water cause cavitation: millions of small bubbles are created, implode and release energy.
The lower the frequency, the larger the bubbles grow before they implode and increase the impact of cleaning. Based on customer-specific applications, we use a frequency of 28 kHz to 80 kHz. From massive, heavily contaminated objects to fragile objects.
We use the sound sine as the engine for our cleaning process and that is why it is important that all elements are synchronized. Through digital synchronization of the ultrasonic elements and custom adjustment of each bath, we can supply the most powerful ultrasonic cleaning machines.
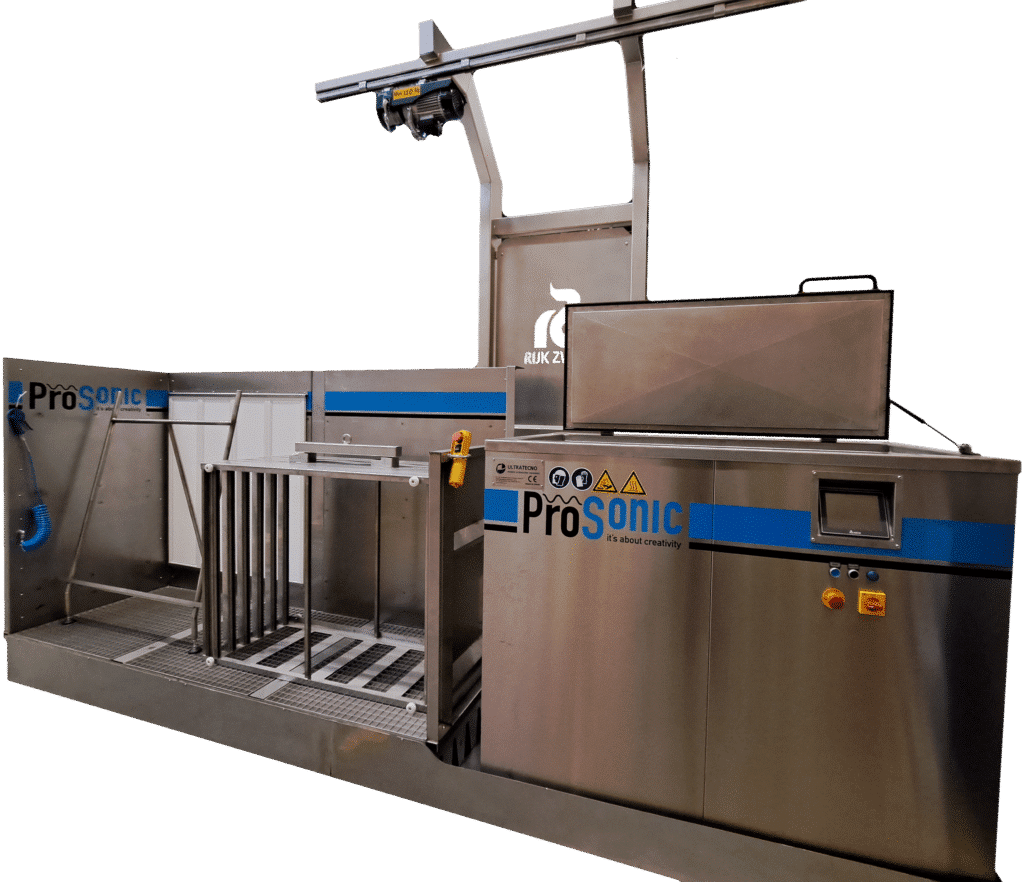
Cleaning with ultrasonics, how?
The tank of the ultrasonic cleaner is filled with a medium. This can be water and chemicals or pure chemicals. Which chemicals are required for daily cleaning is determined in consultation with the customer. After this, the bath is heated. The temperature has 2 functions:
- the loose and soft dirt is released
- it lowers the vapour pressure of the liquid so that cavitation becomes possible.
A powerful ultrasonic wave is sent through this bath, in our case 28 kHz. The sinus locally creates a negative pressure which results in small vacuum bubbles. These vacuum bubbles have a lifespan of half a cycle. This force, better known as cavitation, implodes against the hard surface and is the cleaning effect of the ultrasonic cleaner.
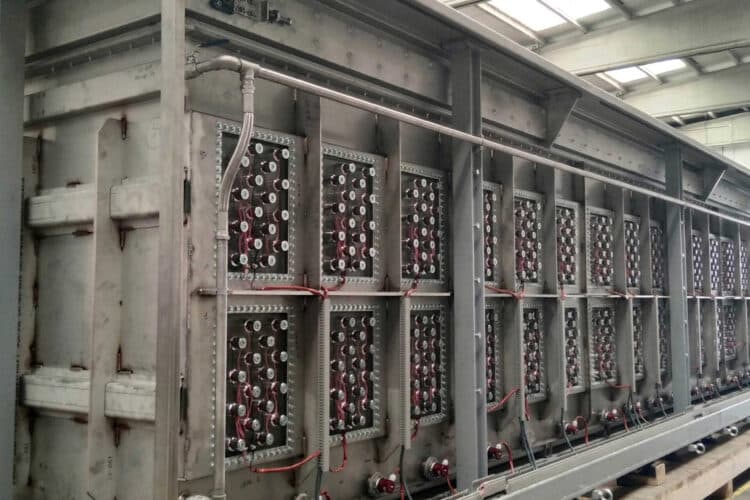
The low frequency of 28 kHz gives a longer build-up time of the vacuum bubble, which makes it larger than at higher frequencies and therefore cleans better.
Higher frequencies up to e.g. 120 kHz are used for ultrasonic cleaning of vulnerable parts and fine contamination such as optics, electronics and medical instruments.
As described above, ultrasonic cleaning is the most effective way to separate contamination from a hard surface. By means of correctly selected power, frequency and controlled cavitation, the surface is not affected. This makes it very suitable for cleaning vulnerable moulds in the plastic injection moulding industry, among other things.