More than 10 years of experience in creative Ultrasonic solutions!
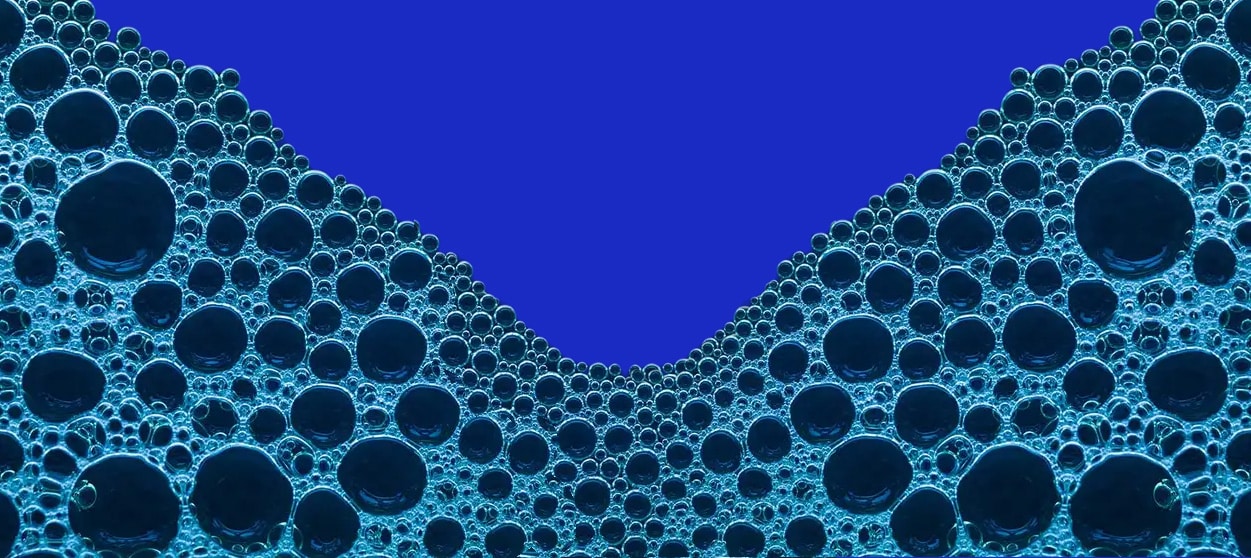
Pressure waves
Using ultrasonic technology, we generate pressure waves which are used to control foam development during the filling of beverages.
Our patented technology makes it possible to limit foam in the bottle neck or headspace during filling. Overflow of foam is prevented without affecting the beverage itself.
The waves allow the foam to implode without affecting the CO2 content in the bottle neck, which keeps the TPO within specifications.
The foam controller can be integrated easily and quickly into all common filling systems. In addition to the beer and beverage industry, this system is used in industrial processes, such as the production of medicines, chemicals, inks and cleaning agents.
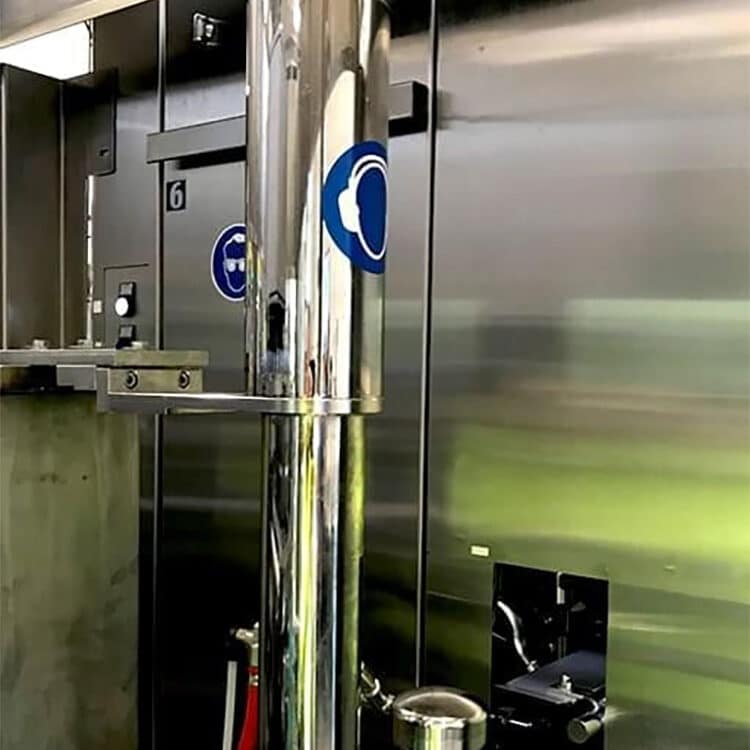
The system
Components
- Control cabinet with generator (within 12 meters of the foam controller).
- Foam controller (place above the filling line).
Features
- Single-phase AC, 100-240V, 12A
- SS AISI316, waterproof (IP67)
- Resistant to CIP cleaning chemicals
- Hygienic surface
- Very low maintenance costs
Beer filling line
- Filler: KHS
- Packaging: 330 ml and 500 ml cans
- Position of defoamer: above the filling line between filler and capper
- Increase in filling speed by approx. 9% from 78,000 to 85,000 cans/h (330 ml) and 66,000 to 72,000 cans/h (500 ml)
- 0.6% reduction in extract loss with faster filling speed
- Reduction in underfill failure by 27%
- No contamination on collars, wire, labels and packaging
- Significant reduction in cleaning costs of the line
CSD filling line
- Filler: Krones
- Packaging: 330 ml and 500 ml cans
- Position of defoamer: above the filling line between filler and capper
- Increase in filling speed from 81,000 to 90,000 cans/h (330 ml) and 60,000 to 72,000 cans/h (500 ml)
- 2.3 ml less product waste per 330 ml can and 2.8 ml less product waste per 500 ml can at faster filling speed
- Elimination of contamination on can ends, labels and packaging
- Increased quality for the end customer